Unlocking the Power of Welding WPS: Strategies for Performance and Security in Fabrication
In the world of construction, Welding Procedure Requirements (WPS) stand as the foundation of welding operations, determining the needed steps for achieving both performance and security in the fabrication process. Recognizing the complexities of WPS is paramount to utilizing its complete capacity, yet many companies struggle to open real power that exists within these files (welding WPS). By diving into the approaches that enhance welding WPS, a globe of enhanced performance and increased safety waits for those happy to check out the nuances of this crucial aspect of construction

Value of Welding WPS
The importance of Welding Procedure Requirements (WPS) in the fabrication market can not be overemphasized. WPS work as a vital roadmap that details the essential steps to guarantee welds are executed consistently and properly. By specifying important criteria such as welding procedures, products, joint layouts, preheat temperatures, interpass temperature levels, filler steels, and post-weld warmth treatment requirements, WPS offer a standard technique to welding that boosts efficiency, high quality, and safety in fabrication processes.
Adherence to WPS aids in attaining uniformity in weld quality, decreasing the probability of flaws or architectural failings. This standardization additionally facilitates compliance with industry laws and codes, making certain that produced structures meet the required safety standards. Moreover, WPS documentation enables welders to replicate successful welding procedures, leading to constant results across various tasks.
Basically, the precise development and rigorous adherence to Welding Treatment Specifications are critical for upholding the honesty of bonded structures, safeguarding versus prospective risks, and upholding the reputation of fabrication firms for providing top quality items and services.
Secret Aspects of Welding WPS
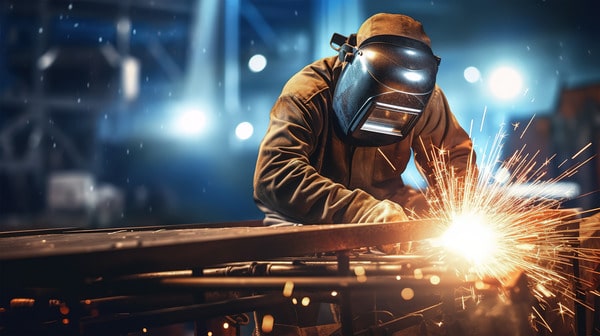
Enhancing Performance With WPS
When maximizing welding procedures, leveraging the essential components detailed in Welding Procedure Specs (WPS) ends up being important for maximizing and enhancing processes performance. One means to enhance efficiency with WPS is by carefully selecting the ideal welding parameters.
Consistently examining and upgrading the WPS to integrate any lessons found out or technological improvements can additionally contribute to performance improvements in welding operations. By welcoming the guidelines established forth in the WPS and constantly seeking methods to maximize processes, producers can attain greater efficiency degrees and premium end results.
Ensuring Security in Manufacture
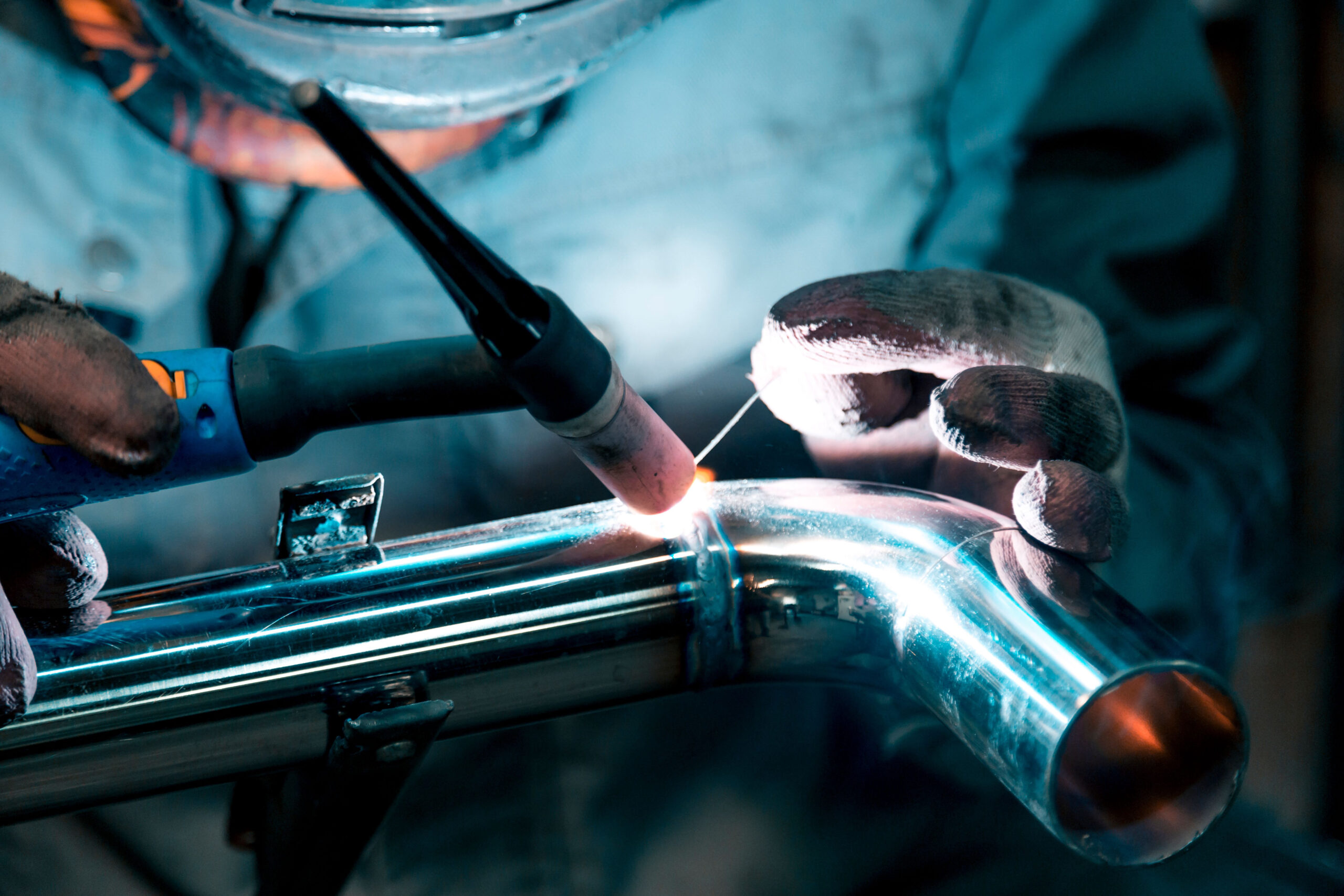
Safety and security basics methods in manufacture play a pivotal role in safeguarding personnel and optimizing operational treatments. Ensuring safety in fabrication involves a multifaceted approach that encompasses various facets of the welding process. One fundamental element is the stipulation of personal safety devices (PPE) customized to the details threats existing in the construction atmosphere. Welders should be geared up with appropriate gear such as headgears, handwear covers, and safety clothes to alleviate risks related to welding activities.
In addition, adherence to appropriate ventilation and fume removal systems is essential in keeping a healthy and balanced work setting. Welding fumes include unsafe compounds that, if inhaled, can position significant wellness threats. Executing effective ventilation measures assists to minimize direct exposure to these dangerous fumes, advertising breathing wellness among employees.
Regular tools maintenance and assessments are also necessary for guaranteeing safety and security in fabrication. Damaged machinery can cause injuries and mishaps, emphasizing the significance of regular checks and timely repair work. By focusing on precaution and cultivating a culture of understanding, manufacture centers can create a safe and effective workplace for their personnel.
Applying WPS Ideal Practices
To boost operational effectiveness and make sure quality outcomes in fabrication processes, including Welding Treatment Spec (WPS) finest methods is paramount. Selecting the suitable welding procedure, filler product, and preheat temperature level specified in the WPS is critical for accomplishing the wanted weld high quality. Ensuring that certified welders with the necessary accreditations bring out the welding treatments according to the WPS guidelines is essential for uniformity and dependability.
Verdict
Finally, welding WPS plays an essential role in making sure efficiency and security in manufacture processes. By concentrating on crucial elements, improving performance, and implementing finest techniques, companies Discover More can maximize their welding procedures. It is important to focus on precaution to avoid mishaps and guarantee a smooth production procedure. By adhering to these approaches, services can unlock the full possibility of welding WPS in their manufacture procedures.
In the realm of manufacture, Welding Treatment Requirements (WPS) stand as the backbone of welding operations, dictating the needed steps for achieving both effectiveness click site and security in the fabrication procedure. By defining necessary specifications such as welding processes, materials, joint designs, preheat temperatures, interpass temperatures, filler metals, and post-weld warm treatment needs, WPS provide a standardized strategy to welding that boosts performance, quality, and safety and security in construction processes.

When enhancing welding operations, leveraging the vital aspects detailed in Welding Procedure Requirements (WPS) comes to be vital for optimizing and simplifying processes productivity. (welding WPS)
Comments on “Why a Welding WPS is Crucial: Enhancing Consistency and Compliance”